Knowledge Hub
Safety Standards for Bulk Material Handling Equipment
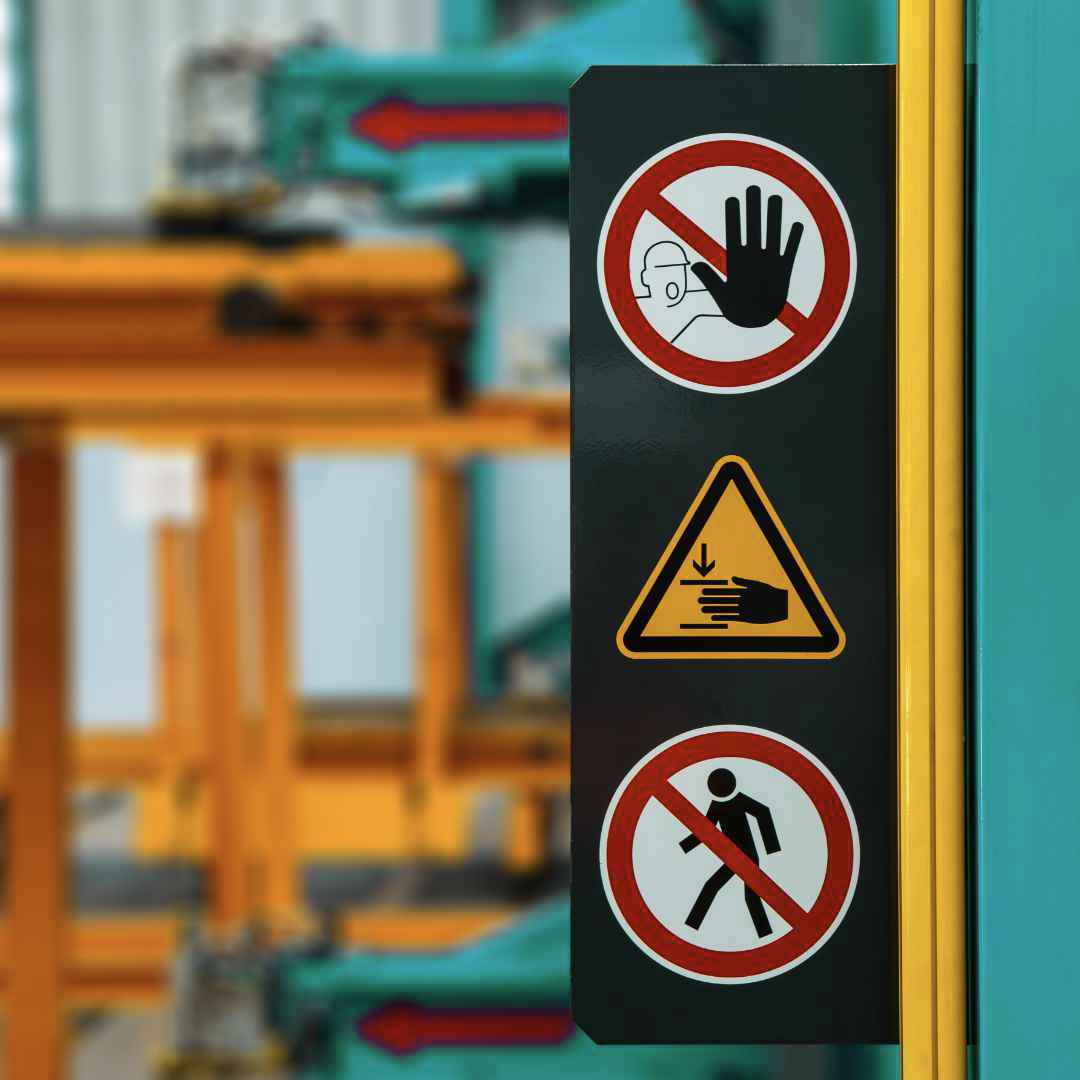
Bulk material handling equipment, essential for managing materials like grain, sand, and ores, comes with unique hazards such as powerful mechanisms, dust-related risks and heavy loads. Implementing robust material handling equipment safety standards is critical to mitigate these risks, protect operators, and ensure equipment longevity.
We explore some of the key safety measures, from professional installation and operator training, to compliance with UK regulations as well as international standards.
What is Bulk Material Handling Equipment?
Bulk material handling equipment refers to the machinery and systems designed to move, store and manage bulk materials. These materials generally take the form of granules, flakes or small particles and may include ores, grain or sand for example. The equipment itself can take various forms, from pneumatic transfer systems to bulk bag discharging stations, each specifically designed to move materials in large volumes.
Due to the high demands placed on these systems, implementing robust safety standards is essential. Each type of equipment presents its own unique hazards, making tailored safety standards necessary to protect both operators and the equipment itself.
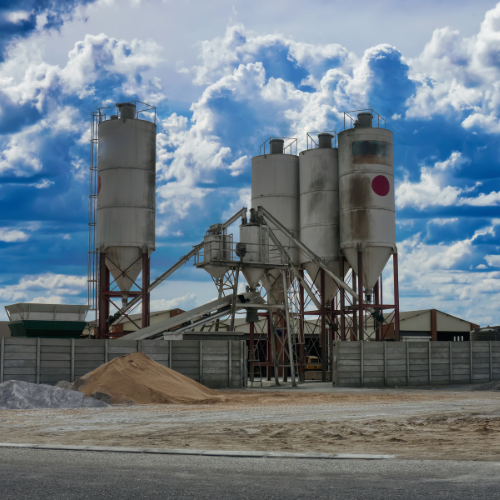
Common Hazards with Material Handling Equipment
Working with bulk material handling equipment poses several potential hazards, including:
- Moving Parts: Components such as conveyor belts, rotating shafts (such as in screw conveyors) and gears present pinch points, which can cause serious injuries if operators are not properly trained or protected.
- Dust: Many materials handled in bulk-like grain, flour or minerals-produce dust, which can lead to respiratory issues and increase the risk of explosions in confined spaces. In October 2024, an explosion in Aurora, Nebraska was caused when dust ignited while corn was being moved from a grain bin to an outdoor pile.
- Lifting Loads: Bulk handling often involves heavy material loads, which, if not managed correctly, can lead to equipment failure or serious injuries if a load is dropped.
Recognising these hazards and implementing appropriate safety standards can drastically reduce the risk of accidents, ensuring a safer work environment and prolonging equipment life.
Key Safety Measures for Bulk Material Handling Equipment
Installation and Commissioning Standards
Professional installation of material handling equipment set the foundation for safe operations. Most safety standards require that equipment be assembled according to the manufacturer’s guidelines and industry best practices, with a focus on stability, secure placement and proper integration with existing systems.
Commissioning for bulk material handling equipment is the final stage in the installation process, designed to ready the system for active use. This phase ensures your equipment operates efficiently by subjecting it to initial testing. During commissioning, the equipment is checked to confirm that safety features are functioning properly, operational performance meets expectations, and all regulatory standards are satisfied.
Operational Safety Training
Safety training can provide clear guidelines for the safe use of material handling equipment. These include protocols for start-up, shutdown and handling of materials, as well as specifications for control systems and machine guarding. Operator training ensures that personnel are familiar with the equipment’s functions, potential hazards and emergency procedures.
Maintenance and Inspection
Routine maintenance and servicing of bulk material handling equipment is vital in identifying potential issues before they escalate. Safety standards in this area mandate regular checks, preventive maintenance and a structured approach to record-keeping.
Keeping maintenance logs helps companies track the performance and condition of each piece of equipment, reducing the likelihood of breakdowns and ensuring that any issues are promptly addressed.
Emergency Stop and Safety Features
Emergency stop mechanisms and safety features are critical components in bulk material handling systems. Standards dictate the inclusion of fail-safes, emergency stops and other safety mechanisms, allowing operators to quickly halt equipment in case of a malfunction or accident. These features are essential for protecting workers and preventing equipment damage, particularly in situations involving heavy loads or potentially hazardous materials.
Material Handling Equipment Safety Standards & Regulatory Bodies
To enforce material handling equipment safety standards, regulatory bodies set out legal standards and guidelines that companies and manufacturers must follow:
Health and Safety Executive (HSE)
The Health and Safety Executive (HSE) is the UK’s primary regulator for workplace health and safety, aimed at preventing work-related injury, illness and fatalities. HSE develops and enforces regulations, provides guidance and conducts research to support safe practices across various sectors, including bulk material handling.
For companies handling bulk materials, HSE offers detailed resources to help employers and employees identify specific hazards, such as dust or heavy loads and implement effective safety controls. These guidelines are essential for ensuring safety in material-heavy operations where risks may be elevated.
UK-Specific Regulations for Bulk Material Handling Safety
Several UK regulations directly impact the safe operation of bulk material handling equipment. Key regulations include:
Health and Safety at Work Act (HSWA)
The Health and Safety at Work etc. Act 1974 (HSWA) serves as the cornerstone of workplace safety in the UK. It mandates that employers, employees and the self-employed maintain a safe work environment. For bulk material handling, this includes requirements for safe systems of work, comprehensive training and adequate supervision to prevent incidents involving heavy machinery and materials.
Employers must ensure, as far as is reasonably practicable, the health, safety and welfare of employees and others impacted by their operations. Employees are also responsible for their own safety and that of others, which is crucial in high-risk settings like material handling. By clearly defining responsibilities, the HSWA creates a structured approach to safety in workplaces where bulk materials are moved and processed.
Provision and Use of Work Equipment Regulations (PUWER)
The Provision and Use of Work Equipment Regulations (PUWER) 1998 require that all equipment used in the workplace is safe, suitable and well-maintained. This regulation is essential for bulk material handling, where equipment reliability is paramount. PUWER emphasises the use of machinery specifically suited to the type and volume of materials being handled, with regular inspections and maintenance to prevent malfunctions.
Additionally, PUWER mandates that only trained personnel operate this equipment, minimising risk in high-stakes environments where heavy materials are moved. Employers must also ensure the presence of protective devices, controls and clear warnings on machinery, all of which contribute to a safer operational environment in material-heavy industries.
Lifting Operations and Lifting Equipment Regulations (LOLER)
The Lifting Operations and Lifting Equipment Regulations 1998 (LOLER) outline essential requirements for the safe use of lifting equipment, highly relevant to bulk material handling where lifting large volumes is routine. LOLER requires that lifting equipment be chosen carefully based on the load, securely installed and maintained through regular checks to ensure safety and efficiency.
For material handling, LOLER underscores that only trained and competent personnel should operate lifting equipment, minimising risks during high-volume lifting operations. By complying with LOLER standards, organisations can prevent incidents related to lifting, enhancing safety and compliance.
International Standards for Global Compliance
For companies operating internationally, standards such as ISO (International Organization for Standardization) and ANSI (American National Standards Institute) offer additional guidance to ensure safety across borders. By adhering to these international standards, companies can meet global safety expectations and create consistent safety practices, particularly in high-risk industries like bulk material handling.
The Role of Preventive Maintenance in Ensuring Safety
Preventive maintenance is essential for maintaining safe and efficient bulk material handling operations. By adhering to preventive and predictive maintenance schedules, companies can preempt equipment failures and minimise the risk of accidents. Recommended maintenance schedules vary by equipment type, but typically include regular checks on moving parts, lubrication, alignment and replacement of worn components.
Proactive maintenance reduces the likelihood of equipment-related incidents, improves efficiency and extends the life of each machine. By investing in routine inspections and predictive maintenance technologies, companies can anticipate issues before they arise, ultimately creating a safer work environment and enhancing productivity.