Knowledge Hub
How to Reduce Dust in Bulk Bag Handling
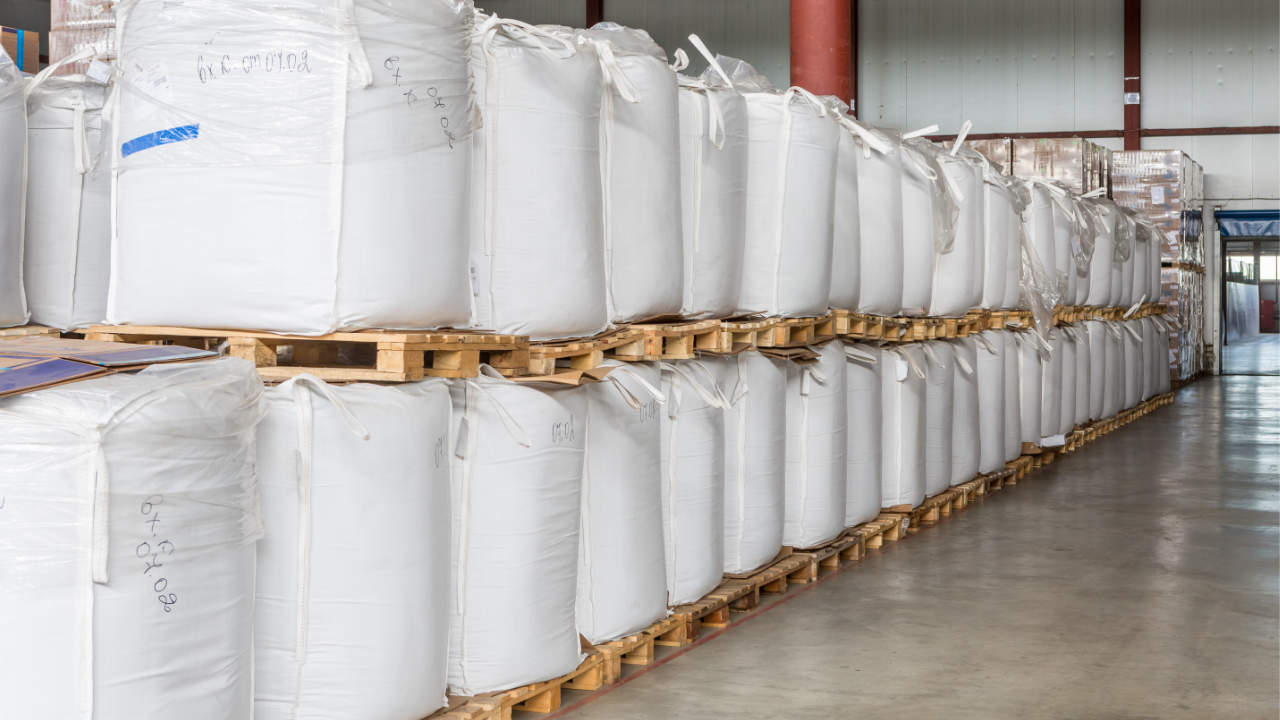
Dust control is a critical aspect of bulk bag handling. Managing dust emissions effectively is essential to maintaining clean and safe environments when handling bulk materials while minimising costs and regulatory risks.
This article explores strategies to reduce dust during both the emptying and filling of bulk bags. By implementing the right equipment and practices, businesses can achieve cleaner and safer operations.
What Causes Dust in Bulk Material Handling?
Dust generation in bulk material handling arises primarily from the physical properties of the materials. Substances like cement, flour and chemicals can easily disperse into the air when disturbed. Other fine powders, lightweight particles and materials prone to static electricity are particularly dust-prone.
Processes like filling and discharging bulk bags can release dust due to high drop heights, rapid flow rates, or displaced air carrying particles into the environment. Handling and transportation, including spillage, mechanical vibrations and environmental factors like wind, can further spread dust.
Dangers of Not Controlling Dust in an Industrial Setting
Inadequate dust control in industrial settings can have severe consequences, particularly when it comes to fire and explosion risks, health hazards, and contamination. These dangers underscore the importance of implementing effective dust management systems.
Fire and Explosion Risks
One of the most catastrophic risks of uncontrolled dust is fire and explosion. Dust from combustible materials, such as flour, can ignite when exposed to heat, sparks or open flames. A recent example of this danger is the Imperial Sugar Refinery explosion in 2008, which occurred in Port Wentworth, Georgia. Accumulated sugar dust ignited, causing a massive explosion that killed 14 workers and injured 36 others. The blast also destroyed large portions of the refinery, with investigations revealing that inadequate dust management and poor housekeeping led to the disaster.
Similar risks exist in industries handling combustible dust, where even settled particles can accumulate over time and trigger secondary explosions. The costs of such incidents-both in human lives and financial losses-are devastating, making proactive dust control an absolute necessity.
Health Hazards
Dust particles, particularly fine powders, can pose serious health risks to workers. Prolonged exposure to airborne dust may lead to respiratory issues such as silicosis, asthma or chronic obstructive pulmonary disease (COPD). Certain dust types can also cause irritation, allergic reactions, or long-term illnesses. Protecting workers from these hazards is not only a legal responsibility but also vital for maintaining a healthy and productive workforce.
Contamination
Dust contamination can compromise product quality, especially in sensitive industries like food, pharmaceuticals and chemicals. Contaminated products can lead to recalls, financial losses, and damage to a company’s reputation. Additionally, dust can spread to surrounding areas, causing environmental pollution and potential breaches of regulations. Addressing these risks requires robust dust containment and extraction systems to ensure a clean and compliant workplace.

Reducing Dust During Bulk Bag Emptying
Bulk bag emptying can be a significant source of dust emissions. Without proper systems in place, material particles can escape during discharge, contaminating the workspace and posing risks to workers and equipment. Implementing the right technologies and techniques can significantly mitigate these challenges.
High-Quality Bulk Bag Emptying Equipment
Effective dust control starts with using specialised equipment. Summit Dynamic Solutions’ Bulk Bag and FIBC Stations are engineered for dust-free operations. These systems ensure that materials are discharged efficiently while preventing dust escape. Their enclosed designs and dust containment features make them ideal for industries handling powders and other fine materials.
These stations are equipped with adjustable hoppers and integrated dust-tight connections, allowing secure attachment to bulk bags. This ensures complete containment of material during the emptying process, reducing cleanup time and improving operational efficiency.
Dust Collection Systems
These systems offer a wide range of benefits, especially when it comes to handling semi-solid materials. Their ability to transport materials of varying densities with ease makes them versatile in industrial settings.
From powdery substances to larger particles, screw conveyor systems can help minimise the risk of material spillage and contamination, maintaining a clean and safe environment. Their adaptability ensures smooth operations and increased productivity, saving time and labour costs.
Reducing Dust During Bulk Bag Filling
Filling bulk bags presents its own set of dust control challenges. As bags are filled, displaced air carries fine particles into the workspace, increasing dust levels. Proper techniques and equipment are necessary to manage this effectively.
Dust-Tight Connections
One of the most effective ways to reduce dust during filling is by ensuring dust-tight connections between the bag and filling equipment. Inflatable collars or clamps can securely hold the bag’s inlet spout in place, preventing dust from escaping. This simple yet effective solution ensures that all material remains contained throughout the filling process.

Ventilation Systems
As air is displaced during filling, it is vital to manage it through proper ventilation. Twin-tube fill heads, for example, can channel dust-laden air into a separate cylinder connected to a dust extraction system. This allows for efficient air filtration, keeping the workspace free of airborne particles.
Bag Materials
The materials used in bulk bags also play a significant role in dust control. Bags made with coated fabrics or equipped with internal liners provide an extra layer of containment, preventing fine particles from escaping through the fabric. Choosing high-quality bags designed for dust-prone materials can make a noticeable difference.
Benefits of Effective Dust Control
Implementing proactive dust control measures delivers numerous advantages, not just for workplace safety but also for operational efficiency and cost savings.
Improved Worker Safety and Morale
Reducing dust levels creates a healthier workplace, minimising respiratory risks for employees. A cleaner environment also boosts morale, as workers feel safer and more comfortable on the job.
Reduced Equipment Wear
Dust particles can accumulate on machinery, causing wear and tear over time. By controlling dust, businesses can extend the lifespan of their equipment, reducing the frequency of repairs and replacements.
Lower Cleaning and Maintenance Costs
A dust-free environment requires less cleaning and upkeep, translating to lower maintenance costs. This also frees up resources for other critical operational tasks.
Avoidance of Fines and Downtime
Regulatory agencies impose strict limits on dust emissions. Effective dust control ensures compliance, helping businesses avoid fines and operational shutdowns. This not only protects the bottom line but also enhances the company’s reputation for environmental responsibility.
Conclusion
Effective dust control in bulk bag handling is more than just a regulatory requirement-it is a vital part of ensuring safe, efficient, and cost-effective operations. By investing in high-quality equipment like Summit Systems’ Bulk Bag and FIBC Stations, businesses can significantly reduce dust emissions, protect worker health, and minimise environmental impact.
The long-term benefits of proactive dust control measures are clear: safer workplaces, extended equipment life, and reduced costs. By implementing these strategies, companies can not only meet compliance standards but also set themselves apart as leaders in operational excellence.
