Knowledge Hub
Introduction to Pneumatic Conveying
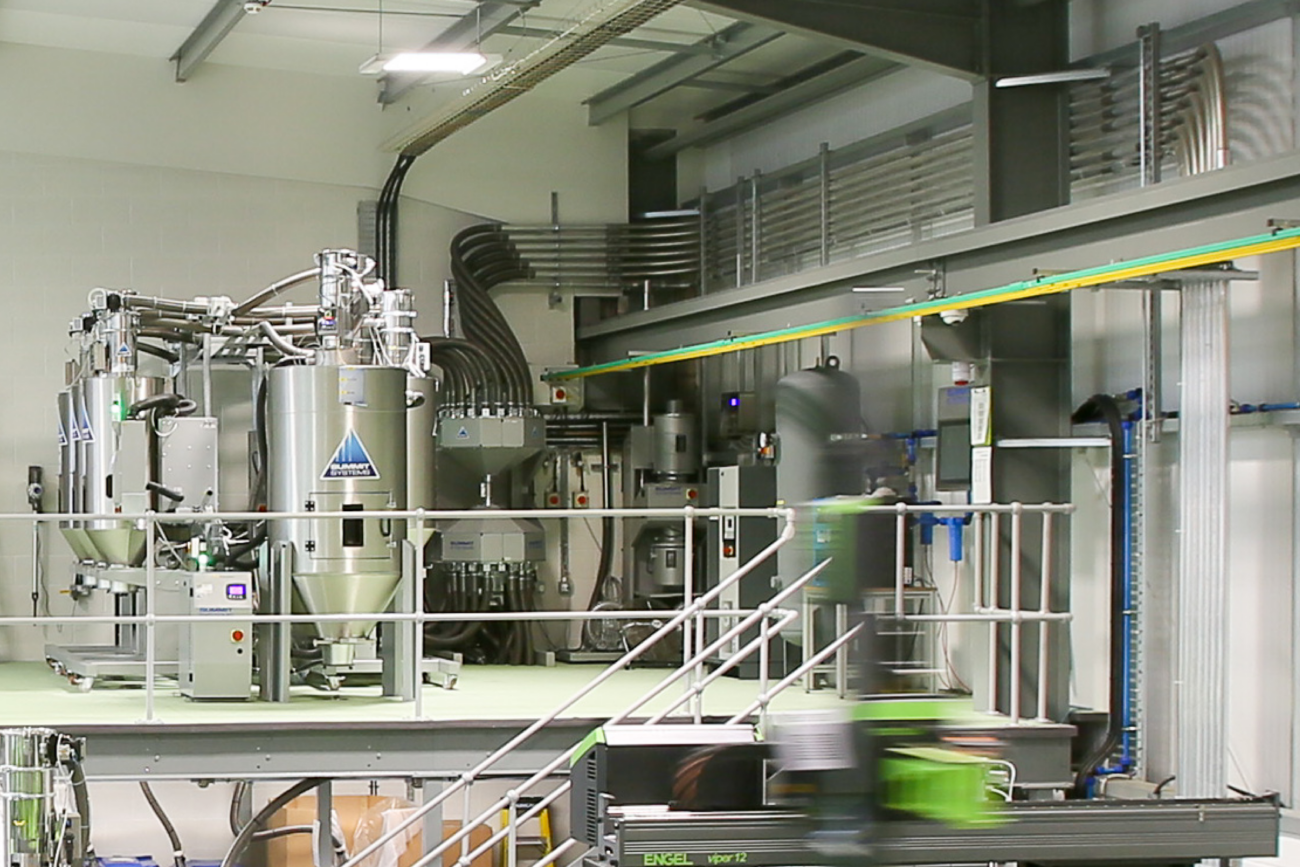
What is Pneumatic Conveying?
Pneumatic conveying is a method of transporting bulk materials through a pipeline using air or gas flow. This system is commonly used for handling dry powders, granules and small particles in industries where contamination-free and efficient material transfer is essential.
Why is it Used in Industries?
Industries rely on pneumatic conveying for its ability to transport bulk materials safely, efficiently and with minimal manual handling. It is particularly useful in sectors that require dust-free environments and strict hygiene standards, such as food processing, pharmaceuticals and chemical manufacturing.
Key Benefits of Pneumatic Conveying Systems
- Enclosed System: Reduces dust and contamination, improving workplace safety and cleanliness.
- Flexibility: Can be installed in complex layouts with vertical and horizontal transport capabilities.
- Low Maintenance: Fewer moving parts lead to reduced wear and tear compared to mechanical conveying systems.
- Efficient and Automated: Minimises human intervention, ensuring consistent material flow.
- Space-Saving: Requires less floor space than traditional mechanical conveyors.
How Pneumatic Conveying Works
The Basic Working Principle of Pneumatic Conveying
Pneumatic conveying operates by using air or gas flow to transport bulk materials through a sealed pipeline system. This system relies on the principle of creating a pressure differential between the start and endpoint, which enables material movement. Depending on the application, pneumatic transfer systems can use either a positive pressure or vacuum method to achieve efficient material flow.
The fundamental mechanism involves an air mover, such as a blower or vacuum pump, which generates the necessary airflow. The material is introduced into the pipeline through a controlled feeding system, ensuring an even and regulated supply.
Once inside the pipeline, the material becomes entrained in the moving air stream, where it is carried towards the designated collection point. A separator or filter then extracts the conveyed material from the air before it exits the system.
Common Components of a Pneumatic Conveying System
- Air Source: Blowers or compressors provide the necessary airflow.
- Pipeline: Enclosed tubes that guide materials from the source to the destination.
- Feeding System: Devices like rotary valves, screw feeders or venturi systems introduce materials into the pipeline.
- Separation Unit: Cyclone separators, bag filters or receivers extract materials from the airstream at the discharge point.
Difference Between Positive Pressure and Vacuum Conveying
Pneumatic transfer systems can be designed to operate using either positive pressure or vacuum pressure.
- Positive Pressure Conveying: Uses compressed air to push materials through the pipeline, ideal for long-distance transport and high-capacity systems.
- Vacuum Conveying: Uses suction to pull materials, preventing dust leakage and commonly used in industries requiring hygienic conditions.
The choice between these methods can depend on factors such as material type, conveying distance and specific manufacturing requirements.
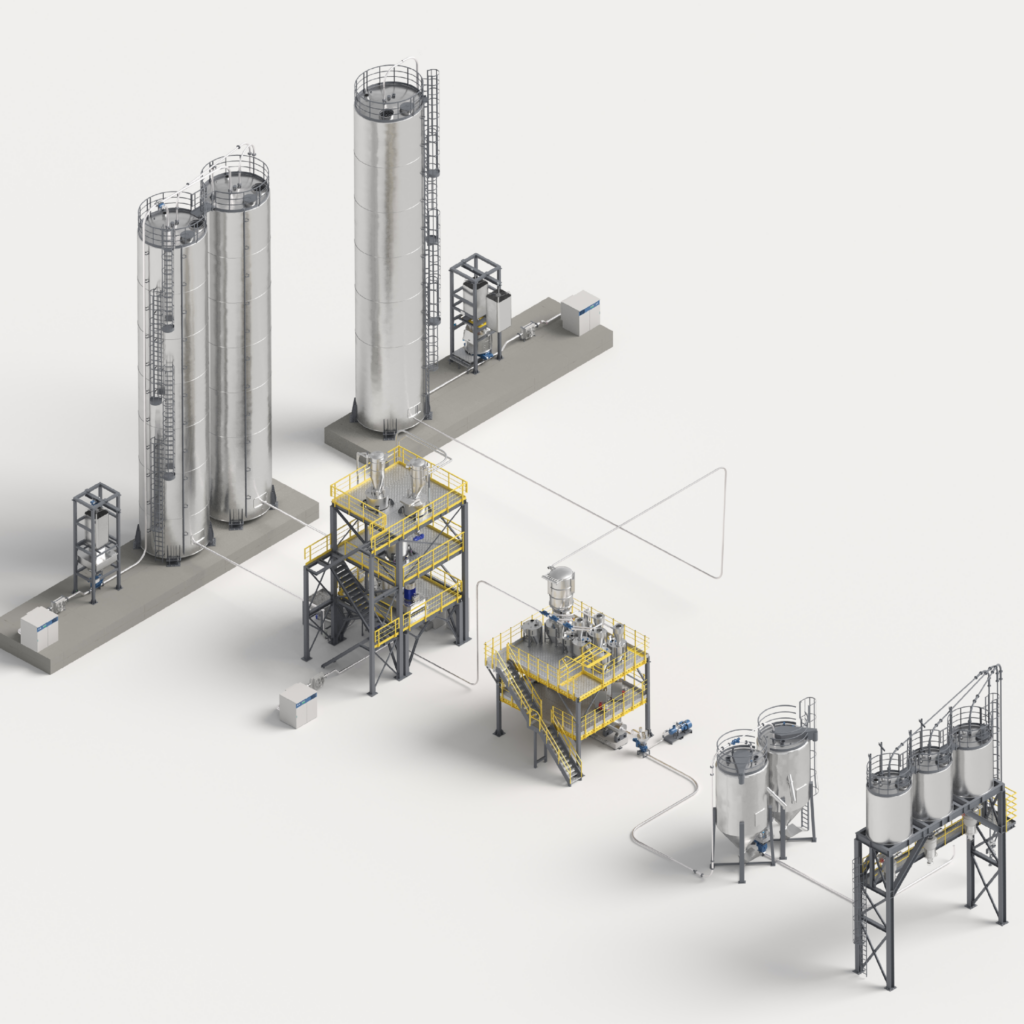
Types of Pneumatic Conveying Systems
Dilute Phase Conveying
Dilute phase conveying is a method where materials are transported in a high-velocity, low-pressure airstream, keeping them suspended throughout the pipeline.
This system ensures continuous movement and prevents material accumulation within the pipeline, making it ideal for handling fine powders and granules. By maintaining an air velocity above the saltation point, dilute phase conveying keeps materials in motion, reducing the risk of clogging or blockages.
The system typically operates with a positive displacement blower or compressed air source, ensuring uniform distribution of materials over long distances. Additionally, because the material is in full suspension, this method minimises the chance of segregation and ensures consistent product quality throughout the process.
Dense Phase Conveying
Dense phase conveying is a low-velocity, high-pressure system that moves materials in a controlled, compacted form to minimise degradation and wear.
This method is particularly suitable for handling fragile or abrasive materials, as it prevents excessive friction and impact that can cause product damage.
The system uses controlled air pulses to push materials through the pipeline in compacted slugs, ensuring a gentle yet efficient transfer. Due to its lower velocity, dense phase conveying also minimises pipeline wear and extends equipment lifespan. It is commonly applied in industries handling fine powders, granules and bulk solids that require precise material handling and controlled flow rates over varying distances.
Why Choose Pneumatic Conveying Systems?
Pneumatic Conveying Compared to Mechanical Conveying:
Less Contamination: Enclosed pipelines prevent exposure to external contaminants.
Reduced Maintenance: Unlike screw or belt conveyors, there are fewer moving parts, reducing mechanical wear.
Greater Flexibility: Easily integrates into existing production layouts and facilities.
Key Benefits:
Dust-Free Operation: Prevents airborne material escape, enhancing worker safety and hygiene.
Flexible Routing: Can transport materials over long distances and complex pathways.
Lower Operational Downtime: Fewer moving parts mean lower maintenance costs and increased uptime.
Industrial Applications of Pneumatic Conveying
Pneumatic conveying systems are widely used across various industries due to their ability to handle bulk materials efficiently while maintaining hygiene and safety standards.
In the food and beverage industry, these systems transport ingredients such as sugar, flour, coffee beans and powdered dairy products. They ensure hygiene compliance by preventing contamination and dust emissions, making them suitable for facilities such as bakeries and ingredient processing plants.
The pharmaceutical industry benefits from pneumatic conveying for the safe handling of fine powders and active pharmaceutical ingredients (APIs). These systems prevent cross-contamination and comply with the stringent regulatory requirements essential for tablet manufacturing and drug formulation.
In the chemical industry, pneumatic conveying is ideal for transporting resins, pigments and various fine chemical powders. By minimising exposure to hazardous materials, these systems ensure worker safety and are commonly used in plastic production, coatings manufacturing and chemical blending facilities.
The construction and cement industry relies on pneumatic conveying for efficiently moving bulk materials such as cement, sand and fly ash. These systems help reduce dust emissions, creating a cleaner and safer work environment. They are frequently employed in concrete batching plants, cement production and material processing units.
The animal feed and agriculture industries can rely on pneumatic conveying systems to transport grains, feed pellets, and powdered supplements. Pneumatic conveying also allows for gentle handling of fragile materials such as soybean meal, wheat bran and corn flour, preventing breakage and maintaining product integrity.
Factors to Consider When Designing a Pneumatic Conveying System
Material Characteristics and Handling Requirements
Understanding the physical properties of the material being conveyed is crucial. Particle size, density, abrasiveness and moisture content can significantly impact system efficiency and performance. The selected system should be capable of handling the material without causing degradation or excessive wear on the equipment.
Distance, Speed and Pressure Considerations
The distance over which materials need to be transported influences the air velocity and pressure required. Longer distances and higher elevations may necessitate greater pressure, while fragile materials may require a lower velocity to prevent damage. Selecting the appropriate parameters ensures optimal performance and material integrity.
Environmental and Regulatory Compliance
Pneumatic conveying systems must adhere to industry regulations regarding safety, hygiene and environmental impact. In sectors such as food, pharmaceuticals and chemicals, compliance with standards like the UK Health and Safety Executive (HSE) and the Food Standards Agency (FSA) are essential. Proper filtration and dust control measures should be in place to minimise emissions and workplace hazards.
Cost, Energy Efficiency and System Layout
Balancing the initial investment with long-term operational savings is key. Energy-efficient blowers and compressors can reduce running costs, while an optimised system layout ensures smooth material flow and minimal maintenance. Future scalability should also be considered to accommodate potential expansions or process modifications.