At Summit Systems, innovation is a guiding principle behind every solution we create. From optimising material flow in process with smart controls and energy efficiency to utilising every kilo of material purchased, our focus is on delivering reliable, future-ready performance. With over 37 years in the plastics industry, Group CEO Mike Jordan — PIA Plastics Ambassador of the Year 2021 — offers an insight into the challenges and opportunities manufacturers face. In this Q&A, he shares his view on where the industry is heading and how Summit Systems is helping shape its future
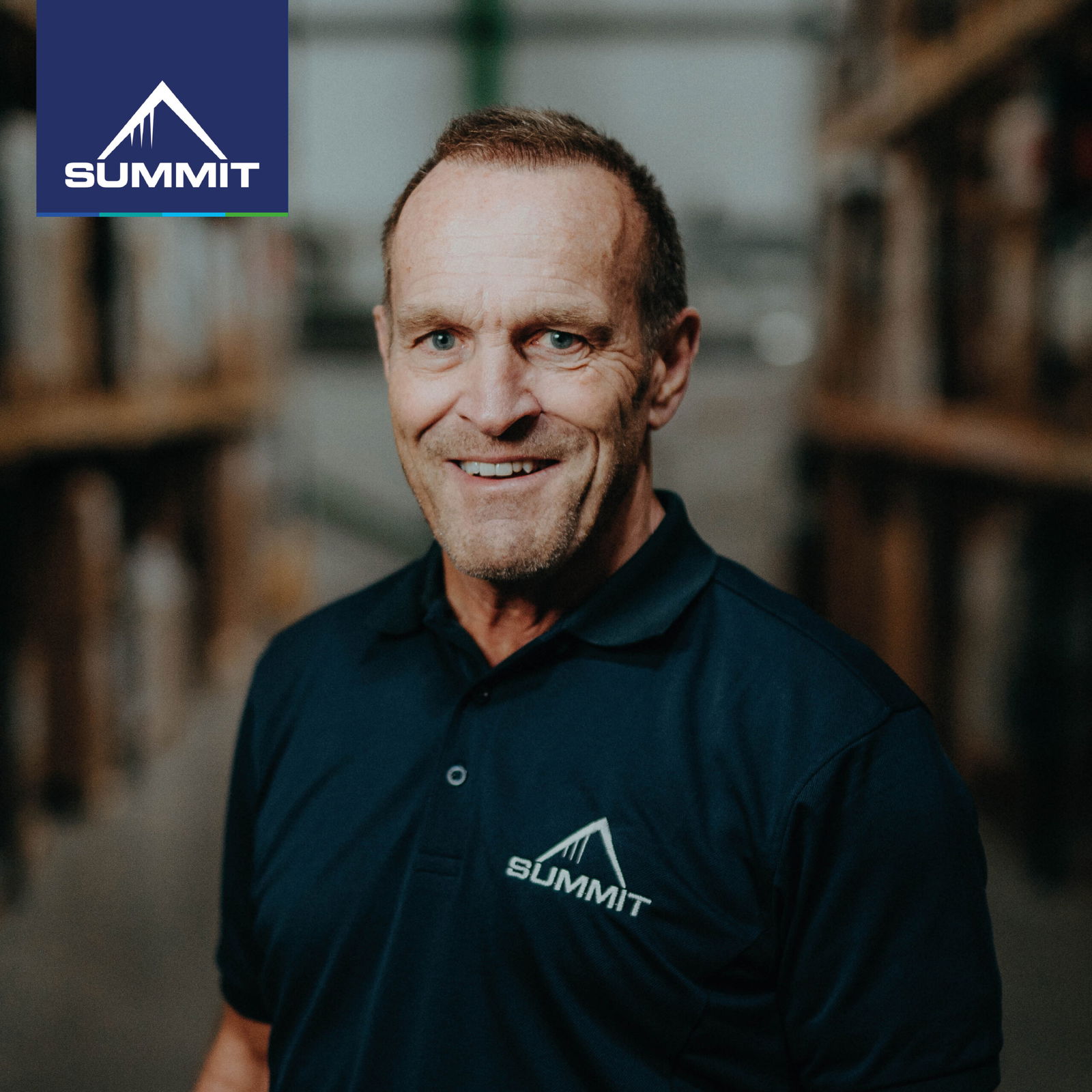
1. What are the most significant challenges in our plastics world in the past five years, and what has been Summit Systems approach?
If I am brutally honest the last 5 years world events have been unstable, from individual country government changes, pandemic, wars and even climate changes – add these up and guesswork comes to mind. You need to be a genius or more likely a “Future Viewer” to predict how polymer prices, currencies, tax regimes or even interest rates will change. This has led to market sectors booming one year to plummeting the next, companies holding investment for months then flood gates opening which makes any business extremely challenging, but as Mary Kay Ash says “Aerodynamically, the bumble bee shouldn’t be able to fly, but the bumble bee doesn’t know it so it goes on flying anyway”. The positive news is that over the past five years, we’ve seen overall a strong investment by companies replacing older technology machines for the latest, more advanced alternatives which are more efficient and advanced which ultimately leads to more quality parts produced per hour with less scrap from the same footprint. With the latest Syncro controlled tool process temperature control and precise blending, the productivity gains have increased dramatically. Just adding these two investments is transformative. A real leap forward in plastics automation is driven largely by Industry 4.0 technologies. Key advancements include smart sensors, IoT connectivity, remote monitoring, and predictive maintenance
2. How is Summit Systems addressing the challenges of integrating legacy equipment with modern automation and data-driven systems?
3. With increasing pressure for sustainable manufacturing, how is automation playing a role in reducing waste, energy use, and environmental impact in plastics processing?
4. What role does predictive maintenance and real-time monitoring play in the efficiency of automated plastics processing lines, and how do your systems enable this?
Material drying using vacuum technology has opened another avenue to further reduce scrap and downtime. At Summit Systems, we’ve integrated these innovations into our equipment and system designs — offering customers enhanced process control, energy savings, and reduced downtime. Our solutions now deliver real-time insights and adaptive control, allowing operators to fine-tune processes with greater accuracy. We’re also developing modular, scalable systems to meet shifting production demands. These upgrades don’t just boost efficiency; they help our customers make more informed decisions, streamline operations, and work more sustainably. Integrating legacy equipment with modern automation is one of the biggest challenges manufacturers face, especially when dealing with older systems. We’ve developed a flexible, modular approach that allows us to retrofit existing machinery with smart sensors, PLC upgrades, and communication interfaces. This enables real-time data capture and seamless integration with newer Industry 4.0 platforms. This approach often significantly reduces the capital cost of a project. Summit is committed to reusing existing equipment by integrating any non-critical components that are perfectly functional. While many suppliers recommend a complete replacement—including equipment that still works—we focus on preserving value. For example, a 15-year-old dryer may need replacing, but the hopper can still be used, offering big savings. Our engineering team works closely with customers to assess compatibility and ensure smooth implementation with minimal disruption. We also provide tailored control systems and cloud-based monitoring tools that unify data from both old and new equipment. The result is a connected, more efficient production environment—without the cost and downtime of full system replacement. Sustainability is no longer optional—it’s an essential part of modern manufacturing. Automation plays a critical role in reducing the environmental impact of plastics processing. By using advanced sensors, smart metering, and energy-efficient controls, automated systems help monitor and minimise material and energy waste at every stage of production. Summit supplies equipment that precisely manages raw material consumption, ensuring accurate dosing, recycling, and minimal over-processing. This significantly reduces scrap rates, lowers energy usage, and enhances overall process stability. We also offer solutions that help customers track their carbon footprint in real-time, so they can make smarter decisions and meet environmental targets more easily. By integrating automation with sustainability goals, manufacturers can boost efficiency and reduce costs while meeting increasingly strict regulatory and customer demands. Our systems empower businesses to make cleaner, data-driven choices that benefit both profit and planet. The truth is, when something goes wrong and production goes down it’s disastrous. I ran a mould shop for 5 years, so I know firsthand that you need urgent solutions. Predictive maintenance and real-time monitoring are essential for keeping plastics processing lines efficient and reliable. Instead of reacting to failures, manufacturers can now anticipate them—cutting downtime, reducing waste, and improving product quality. We use smart sensors and data tools that track variables like temperature, pressure, and energy use. These metrics are analysed in real time, helping spot issues early and schedule maintenance before breakdowns occur. We also offer dashboards and alerts that give teams full visibility, even remotely. This improves responsiveness and keeps systems running at peak performance. BUT, we all know that the best solution is having a magically appearing engineer at the ready 24/7. We also know this is not possible, unless you have a really well-trained team, but this is rare due to the cost and availability of such talents, so we have worked very hard to make this a priority function. We offer full training for those who have the rare talent but backed up by the only genuine 24/7 service team. Summit Systems remains at the forefront of plastics automation, combining innovation and experience to drive smarter, more sustainable manufacturing. As Mike notes, the future is about staying connected, efficient, and ready to meet the evolving needs of the industry